When you're balancing a crank and you go to make a smaller hole larger, the drill always wants to walk around the perimeter of the hole. I find that if I pre-drill to the correct size with a step drill, it eliminates this issue. Adney Brown Performance Crankshaft inc....
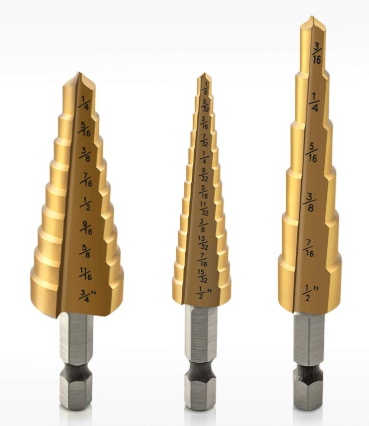