KNOCKING OFF THE EDGES Before installing cam bearings, make sure to chamfer any oil holes and clean up back grooves of any sharp edges. This is especially critical with aluminum blocks. I like to give these areas a little buff on the mounted wheel to finish. This will...
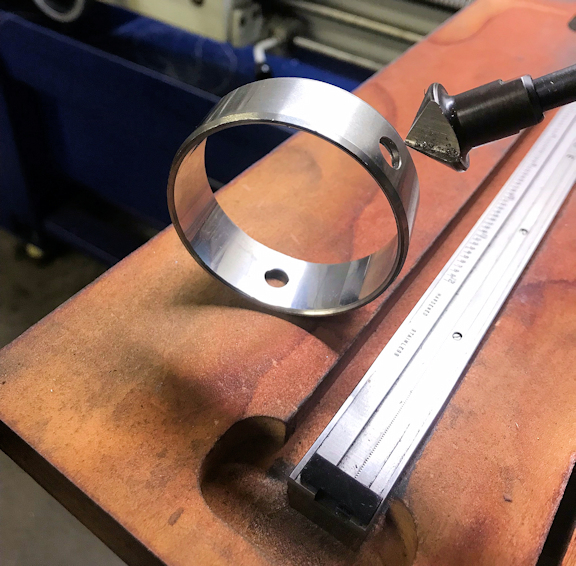