ROTTLER HM3 HONE REPAIR Here is how you can repair your Rottler hone head since Rottler does not service this any longer. Use a Regis part number RSI218. You will need to drill out the top of pinion to remove the expander nut. Then cut the top of the shaft and drill...
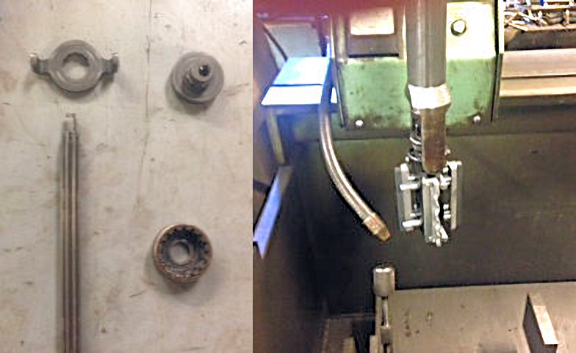